What is RO4350B PCB?
RO4350B PCB | High Frequency PCB Manufacturer.RO4350B PCB is crafted by a leading manufacturer specializing in high-frequency circuitry. Renowned for its exceptional performance in RF and microwave applications, RO4350B PCB ensures superior signal integrity and minimal loss. With meticulous engineering and cutting-edge technology, this manufacturer delivers precision and reliability in every board. Whether for aerospace, telecommunications, or medical devices, their expertise in high-frequency PCB fabrication guarantees optimal functionality and durability. Trust in RO4350B PCB and elevate your projects with unparalleled quality and performance, setting new standards in the realm of advanced electronics.
RO4350B PCB is a high-frequency laminate material with excellent electrical properties and is widely used in electronic applications requiring high-speed signal transmission and low loss. Its unique properties make RO4350B PCB popular in fields such as wireless communications, radio frequency equipment, radar systems and high-frequency electronic equipment.
One of the key features of the RO4350B PCB is its low dielectric loss, which means that virtually no energy is lost during signal transmission. This makes the RO4350B PCB particularly suitable for applications that require the transmission of high-frequency signals over long distances while maintaining signal accuracy and strength. In addition, RO4350B PCB also has excellent thermal stability and dimensional stability, ensuring stable performance under different temperatures and environmental conditions.
The structure of a RO4350B PCB typically consists of multiple copper conductor layers sandwiched between RO4350B substrate layers. This structure not only provides a good signal transmission path, but also enhances the mechanical strength and durability of the PCB. The design of the copper conductor layer can be optimized according to the requirements of the specific application to achieve optimal signal transmission and interference immunity.
In short, RO4350B PCB is known for its excellent electrical performance, stability and reliability, and has become the material of choice for many high-frequency electronic equipment. Its wide range of applications and reliable performance make RO4350B PCB play an important role in modern communications, aerospace, medical equipment and military fields.
How to Design a RO4350B PCB?
RO4350B PCB is an important circuit board material used in high-frequency applications, and its design must be carefully considered to ensure that the final product can meet the high performance and stability requirements. Signal integrity, impedance matching and thermal management are critical factors when designing the RO4350B PCB.
First, signal integrity is one of the key factors to consider during the design process. In high-frequency circuits, signal transmission is affected by wiring length, environmental noise, and signal loss, so measures must be taken to ensure stable signal transmission on the PCB. To maintain signal integrity, designers need to pay attention to the length and direction of signal paths to minimize signal transmission delays and distortion.
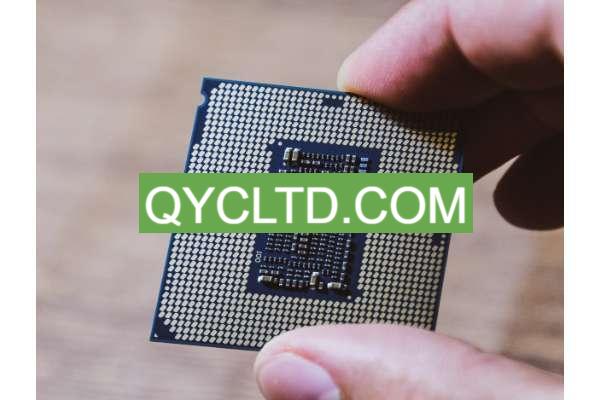
RO4350B PCB | High Frequency PCB Manufacturer
Secondly, impedance matching is also one of the important factors to consider when designing RO4350B PCB. Impedance matching refers to ensuring that the impedance matches between the signal source, transmission line and load to minimize signal reflection and loss. To achieve good impedance matching, designers need to select appropriate transmission line widths and distances and follow prescribed design specifications during layout and routing.
Additionally, thermal management was one of the key considerations in designing the RO4350B PCB. High-power devices and high-frequency circuits generate a large amount of heat during operation. If heat cannot be effectively managed and dissipated, device performance may degrade or even malfunction. Therefore, designers need to reasonably arrange device layout, use heat dissipation devices and thermally conductive materials, and design appropriate ventilation and heat dissipation systems to ensure the stability and reliability of PCBs under various working conditions.
To meet these complex design requirements, top RO4350B PCB manufacturers use advanced CAD software and simulation tools. These tools can help designers simulate and optimize PCB layout and performance, predict potential signal integrity and thermal management issues, and take timely action to correct them. By continuously optimizing layout and design, manufacturers can ensure that each project meets the customer’s unique requirements, providing RO4350B PCB products with high performance and reliability.
In summary, designing the RO4350B PCB requires comprehensive consideration of factors such as signal integrity, impedance matching, and thermal management. Top manufacturers provide RO4350B PCB products with high performance and reliability by continuously optimizing layout and performance to meet the unique requirements of each project through the use of advanced CAD software and simulation tools.
What is the RO4350B PCB Fabrication Process?
The manufacturing of RO4350B PCB is a highly precise process that requires multiple steps to ensure the quality and performance of the final product. From material selection to final inspection, the manufacturer will strictly control every link to ensure the performance and consistency of RO4350B PCB.
First, the first step in manufacturing RO4350B PCB is material selection. RO4350B is a special high-frequency laminate material with excellent electrical characteristics and stability. Manufacturers carefully select RO4350B substrates that meet specifications to ensure the performance of the final product.
Next, the manufacturer pre-treats the substrate, including cleaning and removing surface oxides to ensure good adhesion of the copper layer and surface smoothness. The surface of the substrate is then coated with a layer of conductive material, usually copper, to form the desired circuit pattern.
After the circuit pattern is formed, the manufacturer performs chemical etching or mechanical processing to remove the unnecessary copper layer, leaving the desired circuit structure. This step requires extreme precision and technique to ensure the integrity and accuracy of the circuit.
Next comes the drilling and metallization steps. Manufacturers use precision drill presses to drill holes into PCBs to install electronic components and create connecting pathways. Subsequently, through a metallization process, a metal layer is plated on the PCB surface and hole walls to enhance conductivity and corrosion resistance.
Finally, the manufacturer performs surface treatment and final inspection. During the surface treatment process, the PCB is coated with a protective solder film or other covering to protect the circuitry from environmental factors. The final inspection phase includes electrical performance testing, visual inspection and dimensional measurements of the PCB to ensure it meets quality standards and specifications.
Overall, the RO4350B PCB manufacturing process requires multiple precise steps, each of which is crucial. Manufacturers ensure that the performance and quality of the final product meet customer expectations through strict control of material and process parameters, as well as comprehensive inspection and testing.
How to Manufacturer a RO4350B PCB?
Manufacturing RO4350B PCB requires a series of precise steps and strict quality control to ensure the final product meets high performance and reliability requirements. Here is the basic process for manufacturing a RO4350B PCB:
Material Preparation: First, the manufacturer needs to prepare the RO4350B laminate material along with other necessary materials such as copper foil, backsheet, and chemicals. Ensuring that the quality and specifications of materials meet design requirements is fundamental to the manufacturing process.
Drawing design and preprocessing: Next, based on the customer’s requirements and design specifications, the manufacturer will perform PCB drawing design. During the design stage, it is necessary to ensure the accuracy and consistency of circuit layout, line width, spacing and other parameters. Then, preprocess the drawings, including drawing verification, data conversion and typesetting.
Printing: The copper foil layer of the PCB is manufactured on the substrate using printing technology. The manufacturer will first apply a thin film on the surface of the substrate, and then use photolithography technology to transfer the circuit pattern on the drawing to the surface of the substrate. Subsequently, the unnecessary copper foil is removed through chemical etching or electrochemical methods, leaving the desired circuit pattern.
Multi-layer board stacking: For multi-layer RO4350B PCBs, manufacturers need to stack multiple printed single-layer boards together. This process requires ensuring the alignment accuracy and stacking pressure of each layer to ensure that the final multi-layer board structure is stable and reliable.
Drilling and Metallization: Next, the manufacturer will drill holes into the PCB to mount components and connect circuits between different layers. The hole walls are then coated with a layer of metal through chemical or electroplating methods to enhance conductivity and corrosion resistance.
Surface Treatments and Coverings: PCB surface treatments are used to protect the circuitry, increase durability and solderability. Manufacturers typically apply a layer of solder paste to the PCB surface and then apply a cover layer to the PCB surface via heat pressing or immersion.
Final inspection and packaging: The manufactured RO4350B PCB will undergo strict final inspection, including visual inspection, electrical performance testing, reliability testing, etc. These tests ensure that the PCB meets design requirements and quality standards. Finally, the PCBs are packaged, labeled and classified according to the customer’s requirements for easy transportation and use.
In summary, manufacturing RO4350B PCB requires a combination of advanced technology and strict quality control to ensure the product has excellent performance and reliability in high-frequency electronic applications.
How Much Does a RO4350B PCB Cost?
While RO4350B PCBs offer unparalleled performance, their cost can vary based on factors such as board size, complexity, and quantity. However, working with a trusted manufacturer often provides cost-effective solutions through optimized processes and value-added services.
Cost is an important consideration when choosing a manufacturer for your RO4350B PCB. Different projects have different budget constraints, so it’s critical to understand how to control and optimize costs. First, board size is an important cost factor. Typically, larger sized boards are more expensive because they require more raw materials and production resources. However, by optimizing design and layout, scrap can be minimized, thereby reducing costs.
Secondly, the complexity of the board also affects the cost. Manufacturing costs are typically higher for PCBs with complex routing, multi-layer designs, or special process requirements. These designs may require more processing steps and higher process requirements, thus increasing manufacturing costs. However, by working closely with the manufacturer, the best solution can be found that balances performance needs and cost budgets.
Finally, order quantity also has an impact on costs. Typically, large-volume orders can enjoy lower unit prices because manufacturers can reduce costs through mass production. Additionally, establishing long-term relationships with manufacturers also helps in getting better pricing and offers.
While cost is an important consideration, working with a trusted RO4350B PCB manufacturer delivers even more value. These manufacturers typically have extensive experience and technical expertise and are able to provide professional advice and solutions to meet customer needs. In addition, they provide a series of value-added services such as design optimization, raw material procurement, rapid prototyping and quality control, etc., which help improve production efficiency and reduce overall costs.
So while the manufacturing cost of RO4350B PCB may fluctuate, by working with a trusted manufacturer, a cost-effective solution can be achieved. This partnership not only ensures product quality and performance, but also provides customers with long-term value and competitive advantage.
What materials are RO4350B PCB made of?
RO4350B PCB is primarily composed of RO4350B laminate material, which is widely praised for its excellent stability and reliability in high-frequency applications. RO4350B is a special glass fiber reinforced PTFE (polytetrafluoroethylene) composite material with low dielectric loss and consistent dielectric constant, making it ideal for high frequency electronic equipment.
In addition to RO4350B laminate materials, manufacturers use other key materials to enhance the performance and durability of RO4350B PCBs. Copper is a commonly used conductive material used to form circuit traces and connection points to ensure the stability and reliability of signal transmission. Solder paste is another important material used to connect electronic components to the PCB to achieve circuit integrity and reliability. Good soldering is one of the key factors to ensure the normal operation of electronic equipment. In addition, surface treatment cannot be ignored. It can improve the anti-corrosion performance and welding reliability of PCB and ensure that PCB can work stably under various environmental conditions.
By carefully selecting and optimizing the combination of these materials, RO4350B PCB manufacturers can ensure that their products meet the highest performance standards and meet a wide range of application needs. The quality and use of these materials directly affects the performance, reliability and longevity of the PCB, so manufacturer expertise in material selection and handling is critical. Through continuous research and innovation, manufacturers continue to improve materials and processes to meet increasingly stringent market demands and promote the development and application of high-frequency electronic technology.
To sum up, the performance and reliability of RO4350B PCB benefit from the careful selection and optimization of multiple key materials. The manufacturer’s expertise in material selection, processing and application will provide customers with high-quality products and meet the requirements of various high-frequency electronic devices.
Who manufactures RO4350B PCB?
In today’s highly competitive PCB manufacturing market, finding a good RO4350B PCB manufacturer is crucial. As a representative of technological innovation and quality assurance, our company is proud to be a leader in RO4350B PCB manufacturing. Here are some of our company’s unique advantages:
Technical Expertise: We have an experienced engineering team that is proficient in the design, manufacturing and application of RO4350B PCB. They continually strive for excellence and keep abreast of the latest technological developments in the industry to ensure that our customers remain at the forefront of technology.
Advanced Manufacturing Facilities: Our manufacturing facilities are equipped with state-of-the-art production equipment and technology capable of catering to a wide range of complex PCB manufacturing needs. From automated production lines to precision inspection equipment, we ensure every PCB meets the highest quality standards.
Strict quality control: We adopt a strict quality management system, and every link from raw material procurement to final product delivery is strictly monitored and inspected. Only products that pass strict quality inspection can leave the factory to ensure that every customer gets excellent products.
Customer Customization Services: We understand that each customer’s needs are unique, so we provide customized services to customize PCBs according to customers’ specific requirements. Whether it is complex design or high-volume production, we can provide our customers with the highest quality solutions.
Continuous improvement and innovation: We continue to conduct research and development and innovation, and are committed to providing more advanced and reliable products and services. Through close cooperation and feedback from our customers, we continuously improve and optimize our manufacturing processes to meet our customers’ growing needs.
As a RO4350B PCB manufacturer, we always take customer satisfaction as our mission and are committed to providing customers with the highest quality products and services. Choose us, choose the guarantee of quality and reliability, choose to cooperate with industry leaders, and jointly create a brilliant future!
What are 5 qualities of a good customer service?
In the modern business environment, excellent customer service is one of the keys to business success. Below we’ll explore five key qualities that make up great customer service:
Professionalism: Excellent customer service starts with a professional attitude toward your customers. This means every interaction with customers should be filled with professionalism, including courtesy, respect and accurate messaging. Whether communicating by phone, email, or in person, employees are expected to demonstrate a high level of professionalism to build customer trust and respect.
Prompt response: Prompt response is one of the key factors in customer satisfaction. A good customer service team should be able to respond quickly and efficiently to customer inquiries, complaints or needs. This means establishing effective communication channels to ensure customers can receive timely help and support when needed.
Personalized care: Every customer is unique, so personalized care is one of the important means to improve customer service quality. Understanding customers’ needs, likes and preferences, and providing targeted customized solutions and services will make customers feel valued and cared for, thereby enhancing customer satisfaction and loyalty.
Problem-solving skills: In customer service, it is impossible to avoid problems, but how to respond and solve problems is the key for a company to truly show its value. An excellent customer service team should have the ability to quickly identify problems, solve them effectively, and ensure that customers receive adequate support and satisfactory solutions during the problem-solving process.
Continuous improvement: Excellent customer service is not only about solving current problems, but also about constantly improving and improving service quality to meet the changing needs and expectations of customers. Establishing a feedback mechanism, collecting and analyzing customer feedback, and continuously optimizing service processes and improving service quality will enable the customer service team to maintain its leading position in the industry and win long-term support and trust from customers.
To sum up, professionalism, timely response, personalized care, problem solving and continuous improvement are the five key qualities that make up great customer service. By integrating these traits into your customer service culture, you can win the loyalty and support of your customers and stand out in a competitive market.
FAQS
What are the advantages of RO4350B PCB compared to other materials?
RO4350B PCBs have several distinct advantages over other materials. First, RO4350B material has excellent electrical properties, including low dielectric loss and stable dielectric constant, making it particularly suitable for high-frequency applications. Secondly, RO4350B PCBs have good thermal stability and mechanical properties, allowing them to maintain stability and reliability under various environmental conditions. In addition, the manufacturing process of RO4350B PCBs is relatively mature, providing a reliable foundation for high-precision manufacturing. Overall, RO4350B PCBs enjoy a high reputation in the field of high-frequency electronics and are widely used in wireless communications, radar systems, radio frequency equipment and other fields.
How do I choose the right RO4350B PCB manufacturer for my project?
There are several factors to consider when choosing the right RO4350B PCB manufacturer for your project. First, you should look at the manufacturer’s experience and expertise to see their success stories on similar projects and their knowledge of high-frequency circuit design and manufacturing. Second, you need to evaluate the manufacturer’s equipment and workmanship to ensure it has the technology and facilities necessary to produce high-quality RO4350B PCBs. Additionally, you should also consider aspects such as the manufacturer’s delivery time, service quality, and after-sales support. Finally, communicate with the manufacturer and make sure they can understand and meet the specific needs of your project.
What is the typical lead time for manufacturing a RO4350B PCB?
RO4350B PCB lead times vary based on factors such as manufacturer, order volume, and project complexity. Typically, delivery times for small-volume orders may be shorter than for large-volume orders, and manufacturing times for complex items may also be longer. It is recommended that delivery times be discussed in detail with the manufacturer before working with them and that the delivery date be clearly agreed upon in the contract. Additionally, timely communication and advance planning can also help reduce lead times and ensure projects are completed on time.
What are the advantages of RO4350B PCB compared to other materials?
What are the advantages of RO4350B PCB? First, it has excellent high-frequency performance and is suitable for high-speed signal transmission and low-loss applications. Second, RO4350B material remains stable over a wide temperature range, making it ideal for use in a variety of environmental conditions. Additionally, RO4350B PCB has better mechanical strength and durability compared to other materials, allowing it to operate under extreme conditions for long periods of time without damage.
How do I choose the right RO4350B PCB manufacturer for my project?
There are several key factors that should be considered when choosing a RO4350B PCB manufacturer. First, ensure that the manufacturer has extensive experience and expertise, especially in the high-frequency field. Second, look at the manufacturer’s facilities and equipment to ensure it has advanced production capabilities. Also, check the manufacturer’s quality control system and certifications to ensure the product meets standards and meets your needs. Finally, don’t overlook customer service and communication skills, choose a manufacturer that responds promptly and provides personalized solutions.